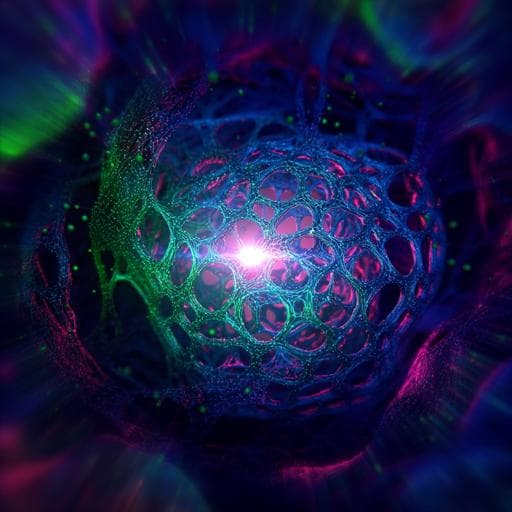
Engineering and Technology
Ultrafast 3D nanofabrication via digital holography
W. Ouyang, X. Xu, et al.
Discover a groundbreaking digital holography-based two-photon lithography platform that revolutionizes the parallel printing of complex 3D nanostructures with remarkable speed and precision. This innovative system achieves a staggering fabrication rate of 2,000,000 voxels/sec and promises to take TPL technology to new heights, validated by large-scale metastructures and optical devices. This cutting-edge research was conducted by Wenqi Ouyang, Xiayi Xu, Wanping Lu, Ni Zhao, Fei Han, and Shih-Chi Chen.
Playback language: English
Introduction
Three-dimensional (3D) nanofabrication is crucial for advancements in nanotechnology. Two-photon lithography (TPL), while highly effective, suffers from slow writing speeds and high costs, limiting its scalability. Current methods, such as multi-beam interference, micro-lens arrays, and diffractive optical elements, are limited to periodic structures due to the lack of individual control over laser foci. Programmable beam shapers offer some control but are hindered by low pattern rates or limited numbers of controllable foci due to insufficient laser power. Projection-based TPL, while offering increased speed, is constrained by its layer-by-layer approach, making it unsuitable for large-scale overhanging structures. This research addresses these limitations by introducing a novel multi-focus TPL platform based on digital holography, aiming to achieve ultrafast 3D nano-printing with high resolution and scalability. The use of a fs regenerative laser amplifier, with its high peak power, enables the generation of numerous independently controllable laser foci, addressing the power limitations of previous techniques. The low repetition rate of this amplifier, however, introduces challenges in polymerization kinetics, requiring a tailored photoresist and optimized printing parameters to ensure high-quality results. This study details the development and characterization of this new platform, demonstrating its capabilities through the fabrication of complex 3D nanostructures.
Literature Review
Two-photon lithography (TPL) has emerged as a powerful technique for 3D nanofabrication, enabling the creation of diverse nanostructures for applications in photonics, robotics, machine design, biomimetic materials, and metamaterials. However, traditional TPL's serial scanning approach severely limits its throughput, making it impractical for large-scale applications. Efforts to enhance speed through multi-focus strategies, such as multi-beam interference, micro-lens arrays, and diffractive optical elements (DOEs), have been partially successful but have limitations in controlling individual foci, thus restricting them to periodic structures. Although programmable beam shapers offer the ability to control individual foci, they are often limited by low pattern rates or a small number of controllable foci due to insufficient laser power. A projection-based TPL approach provides an alternative, but it is inherently limited to layer-by-layer fabrication, preventing the creation of large overhanging structures without support structures. Existing literature highlights the need for a faster, more versatile method that overcomes these limitations, paving the way for the development presented in this study. The use of a high-peak power femtosecond regenerative laser amplifier, while offering the potential for increased throughput, brings its own challenges related to polymerization kinetics, requiring careful consideration of the photoresist and printing parameters.
Methodology
The researchers developed a multi-focus TPL platform utilizing digital holography. A Ti:sapphire fs regenerative laser amplifier (800 nm central wavelength, 1 kHz repetition rate, 100 fs pulse width, 4 W average power) serves as the light source. A digital micromirror device (DMD) displays synthesized holograms, generating multiple laser foci on the Fourier plane. A spatial filter blocks unwanted diffraction orders. The holograms are synthesized using the weighted Gerchberg-Saxton (WGS) algorithm, enabling precise control over the amplitude, phase, and location of each focus. A reflective blazed grating and a 4-f system pre-compensate for angular dispersion introduced by the DMD. A second 4-f system projects the foci onto a custom-designed photoresist under a high-NA oil immersion objective lens. The system allows for random-access 3D scanning, enabling efficient fabrication of low material filling ratio structures. Structures exceeding the DMD's work volume are fabricated through six-axis sample positioning and stitching. A novel photoresist was developed, incorporating a molecule with a large two-photon absorption (2PA) cross-section to suppress multiphoton ionization and promote 2PA at the high peak power of the laser amplifier. The polymerization kinetics were investigated to optimize system parameters. Raman spectroscopy was used to assess the degree of cross-linking (DC) at various pulse energies. A single-pulse TPP fabrication model was developed for low-repetition-rate lasers, focusing on minimizing diffusion effects. The fabrication rate and resolution were optimized by varying the number of laser foci. Experiments were conducted to characterize the impact of factors such as focus proximity and laser power distribution on the quality of the printed structures. Large-scale metastructures, including a cubic metastructure with hundreds of thousands of octahedral truss units, were fabricated to demonstrate the system's high throughput. Mechanical properties of the metastructures were characterized using a rotating rheometer. Additional complex nanostructures, such as arrays of alphabets, nano-dot arrays forming diffractive surfaces, magnetic micro-gears, and micro-lenses, were fabricated to showcase the system's versatility and precision. Characterizations included scanning electron microscopy (SEM), optical microscopy, and Raman spectroscopy. Magnetic micro-gears were fabricated using a magnetic photoresist, demonstrating the system's ability to handle composite materials. The mechanical performance of the fabricated metastructures was evaluated through compression and cyclic loading-unloading tests. Finally, a carbonization process was employed to enhance the mechanical properties of the metastructures.
Key Findings
The study demonstrates a significant advancement in 3D nanofabrication by achieving a volume printing speed of up to 54.0 mm³/h and a resolution of 90 nm (lateral) and 141 nm (axial) using up to 2000 individually controlled laser foci. The system's random-access capability is particularly advantageous for low material filling ratio structures (1–12%), achieving rates as high as 54 mm³/h with 2000 foci. The single-pulse exposure strategy minimizes diffusion effects and maintains high-quality printing even at high focus densities. The custom-designed photoresist exhibits a low polymerization threshold (1.27 nJ) and wide dynamic range, enabling efficient single-pulse polymerization. The fabrication of large-scale metastructures (e.g., a 1.17 mm³ cubic metastructure with over 680,000 octahedral truss units) validates the system's high throughput and precise control. The fabricated metastructures demonstrated significant mechanical resilience, showing over 20-30% compression recovery in cyclic tests. Carbonization further enhanced the stiffness and Young's modulus of the structures. The system's versatility is showcased through the fabrication of various complex 3D nanostructures, including grayscale patterns (alphabets and numbers), diffractive surfaces, micro-lens arrays, and functional magnetic micro-gears capable of complex robotic motions. The ability to fabricate these intricate structures with high precision and speed positions this technology as a promising platform for various applications.
Discussion
The results of this study significantly advance the field of 3D nanofabrication by addressing the critical limitations of existing TPL techniques. The high throughput, resolution, and flexibility of this digital holography-based system offer a compelling solution for scalable manufacturing of complex 3D nanostructures. The system’s ability to fabricate large-scale functional metamaterials with controlled mechanical properties opens new opportunities for material science research and development. The demonstrated fabrication of complex micro-machines, such as magnetic micro-gears, showcases its potential for applications in micro-robotics and other related fields. The achievement of precise grayscale control through independent focus manipulation expands the range of fabricable structures and functionalities. The success of this platform relies on the synergistic integration of a high-peak-power laser amplifier, a custom-designed photoresist, and an advanced digital holography-based DMD scanner. Future work could focus on further increasing the number of controllable foci, exploring new photoresist materials, and integrating the system with advanced control algorithms for even greater speed and precision.
Conclusion
This research presents a groundbreaking multi-focus TPL platform based on digital holography that achieves unprecedented speeds and resolutions in 3D nanofabrication. The platform's capabilities are validated by the successful fabrication of complex large-scale structures and functional micro-devices. The platform offers a significant advancement in additive manufacturing, opening doors for various applications in diverse fields. Future research could explore the use of different laser sources, optimization of the photoresist formulation, and integration of artificial intelligence for advanced process control and design automation.
Limitations
While the system achieves high throughput and resolution, there are some limitations. Over-polymerization can occur with excessive focus density, necessitating careful control of the minimum distance between foci. The custom photoresist requires specialized synthesis, potentially limiting broader accessibility. The system's current setup may be optimized further for even greater scalability by employing a lower magnification objective lens to enlarge the DMD work volume.
Related Publications
Explore these studies to deepen your understanding of the subject.