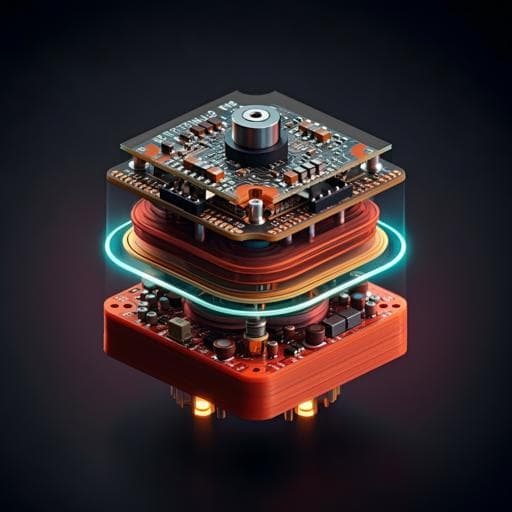
Engineering and Technology
Micro 3D printing of a functional MEMS accelerometer
S. Pagliano, D. E. Marschner, et al.
Discover how a team of researchers from KTH Royal Institute of Technology and EPFL have pioneered a revolutionary 3D-printed MEMS accelerometer using innovative techniques like two-photon polymerization. Their groundbreaking work demonstrates a path towards cost-efficient, custom MEMS devices for varied applications.
Playback language: English
Related Publications
Explore these studies to deepen your understanding of the subject.