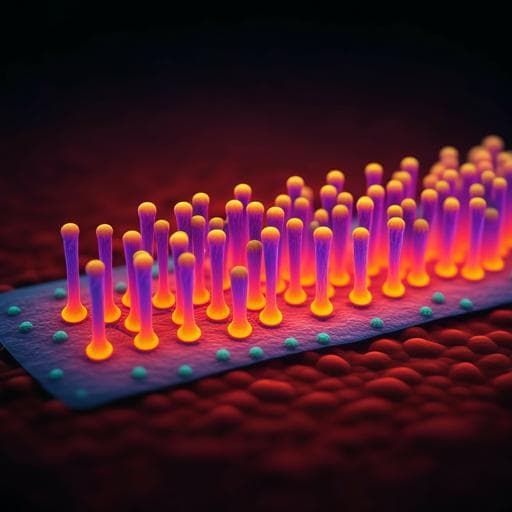
Engineering and Technology
Individually addressable and flexible pressure sensor matrixes with ZnO nanotube arrays on graphene
J. Park, R. Ghosh, et al.
Discover groundbreaking advancements in tactile sensing with the fabrication of high-density, individually addressable vertical zinc oxide nanotube pressure sensor arrays. Conducted by researchers including Junbeom Park and Ramesh Ghosh, this study highlights the remarkable sensitivity and flexibility of piezoelectric sensors on graphene substrates, paving the way for innovative applications in human-electronics interfaces and smart skin technologies.
Playback language: English
Introduction
One-dimensional (1D) piezoelectric semiconductor nanostructures, including nanowires, nanotubes, and nanorods, have shown great potential in nanoelectromechanical energy harvesters, consumer electronics, robotics, and healthcare. These 1D nanostructures can be vertically arranged in small areas to create high-spatial-resolution pressure/force sensor arrays with high sensitivity. Zinc oxide (ZnO) is a particularly attractive material due to its wurtzite structure and piezoelectric properties, making it suitable for sensing platforms in AI and medical devices. However, creating functional tactile sensing devices for next-generation robotics and human-machine interfaces requires large-scale integration of pressure sensor arrays with high spatial resolution, high sensitivity, a wide detection range, fast response, and flexibility. Existing technologies, including resistive, capacitive, and triboelectric sensors, each have limitations. Resistive sensors suffer from high power consumption and temperature dependence. Capacitive sensors can be complex to manufacture and have limited spatial resolution. Triboelectric sensors face challenges in dynamic pressure sensing. Piezoelectric sensors offer advantages such as high sensitivity and fast response, but creating high-density, individually addressable arrays with high resolution (>1000 dpi) using 1D ZnO nanostructures on flexible substrates remains a significant technological challenge. The precise control of dimension and position during the synthesis of high-density 1D ZnO nanostructures is crucial for fabricating these sensor arrays. The use of a two-terminal crossbar electrode array simplifies the fabrication of high-density, individually addressable arrays. Metal-organic chemical vapor deposition (MOCVD) is a promising method for creating high-quality, dimensionally controlled ZnO nanotube (NT) arrays on graphene films. Graphene provides mechanical stability, acts as a flexible conductive layer, and facilitates the lift-off of free-standing ZnO NTs for efficient crossbar microelectrode formation. This research focuses on fabricating individually addressable, flexible, free-standing vertical 1D nanostructure pressure/force sensor arrays using high-quality ZnO nanotube arrays on graphene films. Catalyst-free metal-organic vapor phase epitaxial (MOVPE) growth of ZnO NTs directly on graphene allows for precise control of dimensions and positions. The graphene enables easy lift-off, creating flexible and reliable free-standing sensor arrays. The aim is to achieve high sensitivity, fast response, and a wide detection range, demonstrated through the fabrication and testing of an 8 x 8 matrix of individually addressable sensors. The uniformity and robustness of pressure/force spatial mapping will be investigated by varying pixel size and the number of ZnO nanotubes per pixel.
Literature Review
The introduction extensively reviews existing pressure sensor technologies, highlighting the advantages and disadvantages of resistive, capacitive, triboelectric, and piezoelectric approaches. It emphasizes the limitations of previous piezoelectric ZnO-based tactile sensors, particularly in achieving high spatial resolution and individual addressability in large-scale arrays. The review underscores the need for improved fabrication techniques to overcome these challenges and the potential of using 1D ZnO nanostructures on flexible substrates to create high-performance tactile image sensors. The authors cite relevant studies demonstrating the use of different piezoelectric materials, nanostructures, and heterostructures to improve sensor performance. The use of piezo-phototronic sensors and the work of Liu et al. on high-spatial-resolution piezotronic tactile sensors based on 2D ZnO nanoplatelets are specifically mentioned to illustrate prior attempts to address the challenges in the field. The review sets the stage for the current research by highlighting the gap in the literature regarding the fabrication of high-density, individually addressable, high-resolution piezoelectric ZnO nanotube-based sensor arrays on flexible substrates.
Methodology
The fabrication process begins with the chemical vapor deposition (CVD) growth and transfer of large-area, multilayered graphene films onto a SiO2-coated Si substrate. A thin SiO2 layer is then deposited on the graphene, followed by electron beam lithography to define hole patterns for selective-area growth of ZnO nanotubes. The SiO2 layer is etched, leaving the graphene exposed in the patterned areas. Position-controlled ZnO nanotube arrays are grown on the graphene using metal-organic vapor phase epitaxy (MOVPE) with diethylzinc (DEZn) and O2 as reactants. A polyimide (PI) layer is spin-coated onto the sample to support the ZnO nanotubes during a lift-off process. Oxygen plasma is used to selectively etch the PI layer at the tips of the nanotubes. The graphene layer, along with the ZnO nanotubes and PI layer, is then lifted off from the substrate using Kapton tape. The free-standing ZnO nanotube array is then cured using rapid thermal annealing (RTA). Top and bottom electrode lines (Au and Cr/Au) are formed using electron beam lithography, metal deposition, and lift-off procedures, creating a crossbar electrode array to enable individual addressing of the sensor pixels. The grazing angle metal deposition method is used to conformally coat the ZnO nanotubes with gold. Two different electrode widths are used to integrate different numbers of nanotubes per pixel (3 x 3 and 5 x 5 arrays). The morphology and structure of the ZnO nanotubes are characterized using scanning electron microscopy (SEM) and transmission electron microscopy (TEM). The sensing capabilities of the sensors are characterized by measuring current-voltage (I-V) curves and current-time (I-T) curves under different pressure conditions. Mechanical force and a controlled flow of inert argon gas are used to apply pressure to the sensors. The spatial resolution of the sensor array is determined by the periodicity of the crossbar electrodes, measured in dots per inch (dpi).
Key Findings
High-quality ZnO nanotube arrays with diameters of 500 nm and lengths of 9-10 μm were successfully grown on CVD graphene layers using selective-area MOVPE. The nanotubes exhibit interconnected ultrathin walls, enhancing their robustness. TEM analysis confirmed the high crystallinity of the ZnO nanotubes. SEM images showed conformal gold coating on the ZnO nanotubes, forming Schottky contacts at the top and ohmic contacts at the bottom. Devices containing single nanotubes, small arrays (3 x 3, 5 x 5), and larger arrays (250 x 250) of ZnO nanotubes exhibited excellent piezoelectric responses to small pressures, demonstrating high sensitivity, fast response, and a wide detection range. An 8 x 8 matrix of individually addressable sensors was successfully fabricated and tested. The study investigated the uniformity and robustness of spatial pressure/force mapping by varying pixel size and the number of ZnO nanotubes per pixel. A high spatial resolution of 1058 dpi was achieved for a Schottky diode-based force/pressure sensor on a flexible substrate. The free-standing sensor arrays demonstrated excellent flexibility and electrical robustness for high-resolution tactile imaging.
Discussion
The results demonstrate the successful fabrication of high-performance, flexible, and individually addressable pressure sensor arrays based on ZnO nanotubes grown on graphene. The achieved spatial resolution of 1058 dpi significantly surpasses that of many existing tactile sensors. The use of a crossbar electrode configuration allows for simple and effective individual addressing of the sensor pixels, making the fabrication process scalable for large-area arrays. The excellent flexibility and robustness of the free-standing sensors open up possibilities for various applications in wearable electronics and flexible devices. The high sensitivity, fast response, and wide detection range make these sensors suitable for a broad range of applications requiring precise pressure/force sensing. The findings address the challenges in creating high-resolution, individually addressable piezoelectric sensors by demonstrating a novel fabrication approach based on controlled growth and lift-off of ZnO nanotube arrays on a flexible graphene substrate. This work advances the field of tactile sensing technology and provides a promising platform for developing next-generation flexible electronics.
Conclusion
This research successfully fabricated individually addressable, flexible pressure sensor arrays using ZnO nanotubes on a graphene substrate. The high spatial resolution (1058 dpi), sensitivity, and flexibility demonstrated open significant possibilities for applications in human-electronics interfaces, smart skin, and micro/nanoelectromechanical systems. Future research could focus on further improving the sensitivity, expanding the detection range, and exploring integration with advanced signal processing techniques for real-time tactile imaging applications. Investigating different electrode materials and exploring the use of other 1D nanomaterials could also enhance the performance and expand the capabilities of these sensors.
Limitations
While the study achieved high spatial resolution, further optimization of the fabrication process may be needed to improve the uniformity of sensor response across the entire array. The long-term stability of the sensors under repeated bending and pressure cycles should be further evaluated. The current study primarily focused on static and quasi-static pressure sensing; the response of these sensors to dynamic pressure changes needs more investigation. The influence of temperature and humidity on sensor performance also warrants further study.
Related Publications
Explore these studies to deepen your understanding of the subject.