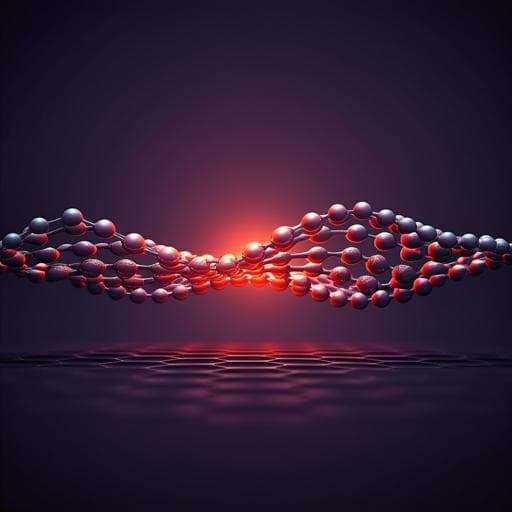
Engineering and Technology
Elastic straining of free-standing monolayer graphene
K. Cao, S. Feng, et al.
This innovative study explores the remarkable elastic properties and stretchability of single-crystalline monolayer graphene, revealing impressive results such as a Young's modulus nearing 1 TPa and tensile strength around 50-60 GPa. Conducted by Ke Cao and colleagues, the findings promise significant advancements in flexible electronics and mechatronics.
Playback language: English
Related Publications
Explore these studies to deepen your understanding of the subject.