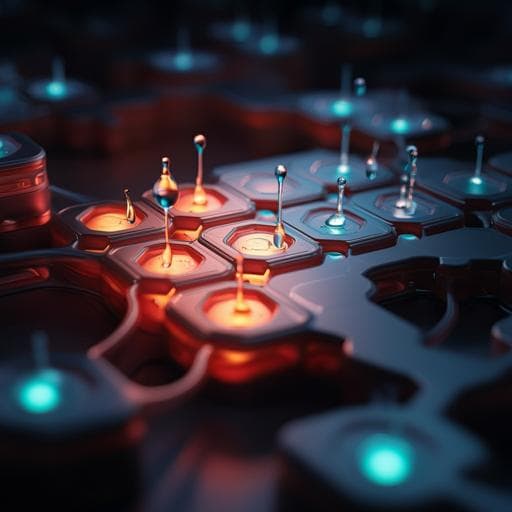
Engineering and Technology
3D free-assembly modular microfluidics inspired by movable type printing
S. Huang, J. Wu, et al.
This groundbreaking research presents a novel 3D free-assembly modular microfluidics scheme, inspired by movable type printing. It features rapid prototyping and small batch production of disposable microfluidic chips, enabling advanced applications like concentration gradient generation and drug screening, all developed by a team from the University of Shanghai for Science and Technology and the Shenzhen Institute of Advanced Technology.
Playback language: English
Related Publications
Explore these studies to deepen your understanding of the subject.