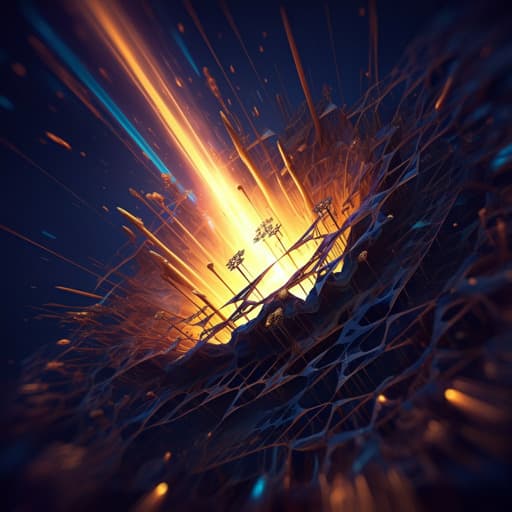
Engineering and Technology
Ultrafast 3D nanofabrication via digital holography
W. Ouyang, X. Xu, et al.
Experience the cutting edge of 3D nanoprinting with our novel digital holography-based two-photon lithography platform! Developed by Wenqi Ouyang and colleagues, this system achieves a staggering 2,000,000 voxels per second while maintaining an impressive resolution of 90 nm. Discover how we’re pushing the limits of fabrication technology beyond conventional laboratory prototyping.
Playback language: English
Related Publications
Explore these studies to deepen your understanding of the subject.