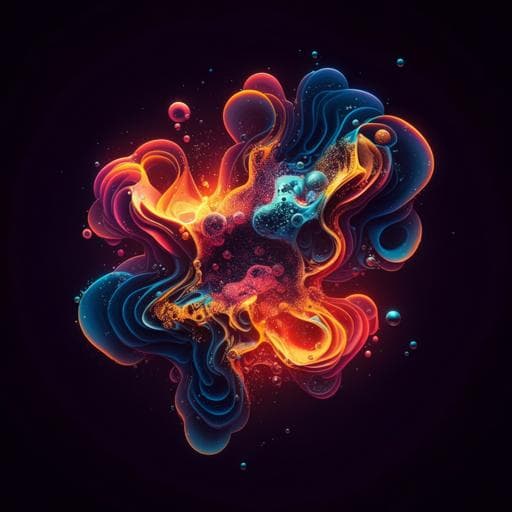
Engineering and Technology
Twisted fiber microfluidics: a cutting-edge approach to 3D spiral devices
S. Kato, D. W. Carlson, et al.
Discover a revolutionary method for creating 3D spiral microfluidic devices using a miniaturized thermal drawing process. Conducted by Shunsuke Kato, Daniel W. Carlson, Amy Q. Shen, and Yuanyuan Guo, this research opens the door to advanced applications in drug delivery and diagnostics.
Playback language: English
Related Publications
Explore these studies to deepen your understanding of the subject.