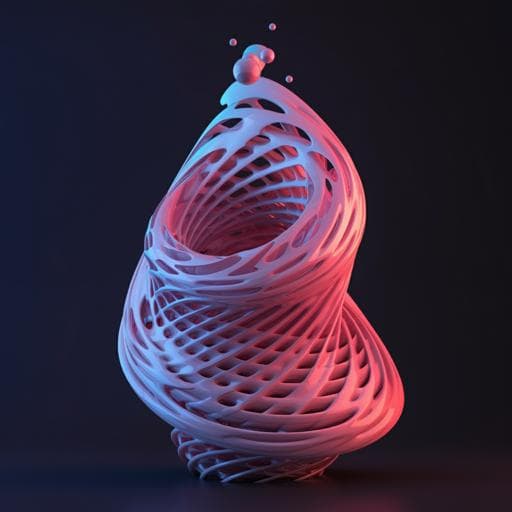
Engineering and Technology
Shape morphing of plastic films
F. Zhang, D. Li, et al.
Discover a groundbreaking method for transforming homogeneous plastic films into intricate 3D structures from their 2D forms. This innovative approach utilizes controlled peeling to create responsive geometries, opening up new possibilities in 3D device fabrication. The research was conducted by Feilong Zhang, Dong Li, Changxian Wang, Zhihua Liu, Man Yang, Zequn Cui, Junqi Yi, Ming Wang, Ying Jiang, Zhisheng Lv, Shutao Wang, Huajian Gao, and Xiaodong Chen.
Playback language: English
Related Publications
Explore these studies to deepen your understanding of the subject.