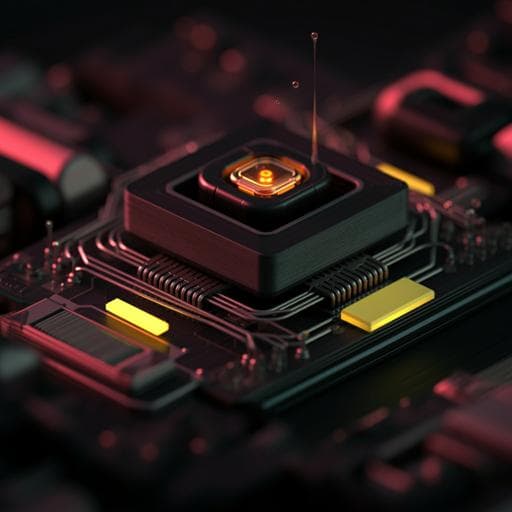
Engineering and Technology
Programmed multimaterial assembly by synergized 3D printing and freeform laser induction
B. Zheng, Y. Xie, et al.
Discover the groundbreaking freeform multimaterial assembly process (FMAP) that revolutionizes how we fabricate functional 3D objects by combining 3D printing and freeform laser induction. This innovative approach introduces versatile applications in circuits, sensors, and more, crafted by a talented team of researchers including Bujingda Zheng, Yunchao Xie, Shichen Xu, Andrew C. Meng, and others from the University of Missouri and Rice University.
Playback language: English
Related Publications
Explore these studies to deepen your understanding of the subject.