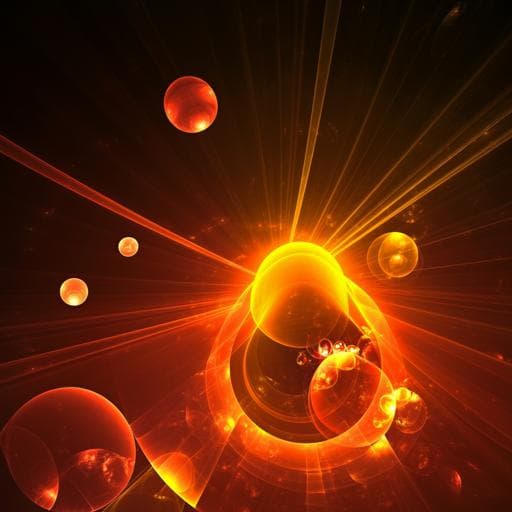
Engineering and Technology
High performance temperature difference triboelectric nanogenerator
B. Cheng, Q. Xu, et al.
Discover how Bolang Cheng, Qi Xu, Yaqin Ding, Suo Bai, Xiaofeng Jia, Yangdianchen Yu, Juan Wen, and Yong Qin have engineered a groundbreaking temperature difference triboelectric nanogenerator (TDNG) that significantly enhances electrical output in high-temperature conditions, achieving unprecedented performance metrics through innovative design.
Playback language: English
Introduction
Triboelectric nanogenerators (TENGs) are devices that harvest mechanical energy and convert it into electrical energy through contact electrification and electrostatic induction. They have shown promise in various applications, including self-powered sensors and energy harvesting. However, a major limitation of TENGs is their performance degradation at high temperatures (>260 K), primarily due to thermionic emission, where electrons escape from the friction layer, reducing charge storage and output. Previous research has focused on material selection, structural optimization, and charge injection techniques to improve TENG performance. Current density records have been achieved using methods such as pumping TENGs (25.2 µA cm⁻²), self-charge excitation TENG systems (28.8 µA cm⁻²), vacuum operation (57 µA cm⁻²), artificial prior-charge injection (90 µA cm⁻²), electric double-layer structures (305 µA cm⁻²), and ferroelectric materials (350 µA cm⁻²). This paper explores a novel approach to mitigate the negative effects of high temperature by exploiting the temperature difference between two friction layers. The concept is based on the observation that a temperature difference facilitates electron transfer from a hotter material to a cooler material, potentially enhancing charge density. While nanoscale studies have demonstrated this effect using atomic force microscopy, its implementation in macroscopic TENGs remains a challenge due to heat exchange between layers and with the environment. This research aims to design, fabricate, and characterize a TENG that takes advantage of temperature difference to enhance its performance in high-temperature environments, potentially enabling applications in areas such as automobile engine monitoring and energy harvesting from temperature gradients.
Literature Review
The literature extensively documents the performance limitations of TENGs at elevated temperatures. Studies have shown a significant decrease in output with increasing temperature due to enhanced thermionic emission. The electron thermionic emission phenomenon, where electrons overcome the potential barrier and escape from the material, has been identified as the main cause of this temperature-dependent performance degradation. Several research efforts have attempted to address this challenge. For instance, techniques such as quenching down electron thermionic emission through material engineering have been explored. Additionally, the impact of temperature differences on nanoscale electron transfer processes has been investigated. These studies showed that temperature differences can facilitate electron transfer, leading to improved charge density within a specific temperature range. However, these nanoscale findings haven't been effectively translated into macroscopic TENG designs. This paper bridges this gap by demonstrating a device that successfully utilizes the temperature difference for enhanced energy harvesting.
Methodology
This study employed both theoretical modeling and experimental fabrication. The theoretical analysis involved developing an electron-cloud-potential-well model to explain electron transfer and dissipation processes under temperature differences. The model considers two competing factors: the enhanced electron transfer from the hotter to the cooler layer and the increased thermionic emission from the cooler layer. Numerical simulations using COMSOL software were conducted to verify the model's predictions. Two equations are introduced to describe the relationship between the surface charge density (σ) and the temperature of the cooler friction layer (T₁), and the relationship between C (a material-related factor) and T₀ (temperature). The relationship between the surface charge density of the TDNG (σTDNG) and ΔT (temperature difference) is expressed using a derived equation incorporating both electron transfer and thermionic emission. The influence of thermal conductivity on the temperature of the cooler layer and the surface charge density is also investigated. A formula to describe the relationship between the voltage output (V(t)) and ΔT is derived using classical electrodynamics. Experimentally, a TDNG was designed and fabricated with a hotter and cooler part, each consisting of three layers: friction layer, electrode film, and a temperature control system. The friction layers were fabricated using reactive ion etching of Kapton film (cooler part) and chemical reactive etching of aluminum foil (hotter part) to create nanostructures that increased the surface area. The temperature control involved a thermostat heater and a water-cooling system. A linear motor drove the TDNG for performance testing. The output voltage and current were measured at different temperature differences. Furthermore, thermally stimulated discharge (TSD) measurements were performed to quantify the accumulated charges on the Kapton film at various temperature differences. The surface potential of the Kapton was also measured. Various material combinations for the friction layers (Al-Kapton, PA-6-Kapton, Cu-Kapton, Fe-Kapton, and Al-PTFE) were investigated to optimize performance. Finally, a wind-driven TDNG was designed and tested to demonstrate its practical application on a high-temperature surface.
Key Findings
The study's key findings demonstrate a significant enhancement of TENG performance by introducing a temperature difference between the friction layers. Numerical simulations predicted that the surface charge density would increase and then decrease with increasing ΔT, indicating an optimal temperature difference for maximum output. The experimental results validated this prediction. With a 145 K temperature difference, the Al-Kapton TDNG exhibited a 2.7-fold increase in open-circuit voltage (858 V compared to 314.5 V at 0 K ΔT), a 2.2-fold increase in short-circuit current (20 µA compared to 8.98 µA), and a 3.0-fold increase in surface charge density (58.8 µC m⁻² compared to 19.6 µC m⁻²). The output power increased by 4.9 times (206.7 µW compared to 42.2 µW). The maximum current density reached 443 µA cm⁻², surpassing the previously reported record of 350 µA cm⁻² by 26.6%. TSD measurements and surface potential analysis confirmed that the temperature difference enhances charge accumulation in the cooler friction layer. The optimal temperature difference varied depending on the material combination, with 145 K being optimal for Al-Kapton and 90 K for Al-PTFE. By optimizing friction materials and parameters (Al-PTFE), an average peak open-circuit voltage of 1.8 kV and an average peak short-circuit current density of 480.3 µA cm⁻² were achieved. A wind-driven TDNG successfully powered LEDs and a temperature-humidity sensor, showcasing the practical applicability of this approach.
Discussion
The results demonstrate that the temperature difference between the friction layers is a critical factor influencing the output of TENGs. The enhanced performance stems from a balance between the increased electron transfer from the hotter to the cooler layer and the thermionic emission from the cooler layer. An optimal temperature difference maximizes the net charge accumulation on the cooler layer. This work significantly advances the understanding and application of TENGs in high-temperature environments. The ability to generate higher power outputs at elevated temperatures opens up numerous possibilities for practical applications, overcoming a critical limitation of traditional TENG designs. The findings support the potential for harvesting energy from waste heat and utilizing temperature gradients for power generation.
Conclusion
This study successfully demonstrated a high-performance TDNG that leverages a temperature difference to overcome the limitations of conventional TENGs at high temperatures. The optimized device achieved record-breaking current density, exceeding previous reports. The results highlight the importance of temperature difference management in enhancing TENG performance. Future research could explore more advanced materials with tailored thermal and electrical properties to further optimize TDNG performance. Investigation into different temperature gradient configurations and integration with other energy harvesting techniques could also lead to innovative applications.
Limitations
The current study focused on specific material combinations and temperature ranges. Further research is needed to investigate the effect of temperature differences on a wider range of materials and operating conditions. The wind-driven TDNG demonstration was a proof-of-concept; optimization of the design and integration into real-world applications require further development. The theoretical model simplifies some aspects of the complex interactions between the friction layers; more sophisticated models could improve accuracy.
Related Publications
Explore these studies to deepen your understanding of the subject.