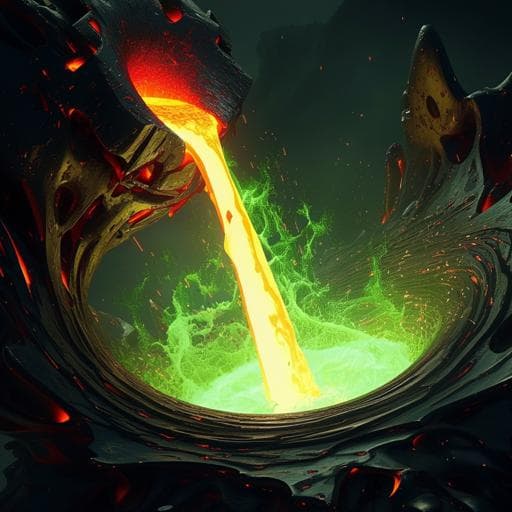
Engineering and Technology
Green steel from red mud through climate-neutral hydrogen plasma reduction
M. Jovičević-klug, I. R. S. Filho, et al.
Discover a groundbreaking method by Matic Jovičević-Klug, Isnaldi R. Souza Filho, Hauke Springer, Christian Adam, and Dierk Raabe that transforms red mud, a waste of alumina production, into green steel using fossil-free hydrogen-plasma reduction. This innovative process not only aids in sustainable red mud disposal but also significantly reduces CO2 emissions associated with steel production.
Playback language: English
Related Publications
Explore these studies to deepen your understanding of the subject.