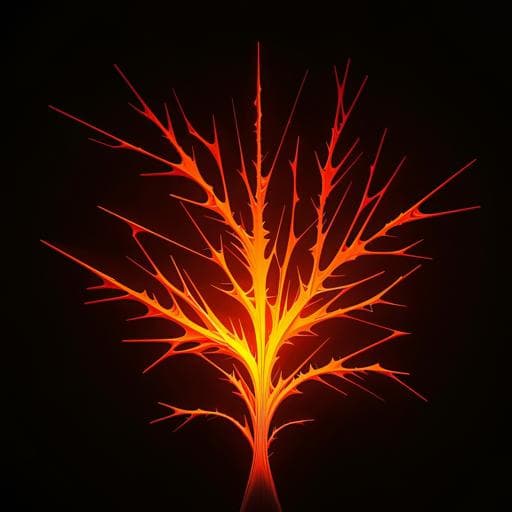
Engineering and Technology
Complexity of crack front geometry enhances toughness of brittle solids
X. Wei, C. Li, et al.
Discover how the intricate geometry of crack fronts in brittle solids significantly influences their toughness, as revealed by a study conducted by Xinyue Wei, Chenzhuo Li, Cían McCarthy, and John M. Kolinski. This groundbreaking research challenges existing theories and offers exciting implications for materials science and engineering.
Playback language: English
Related Publications
Explore these studies to deepen your understanding of the subject.