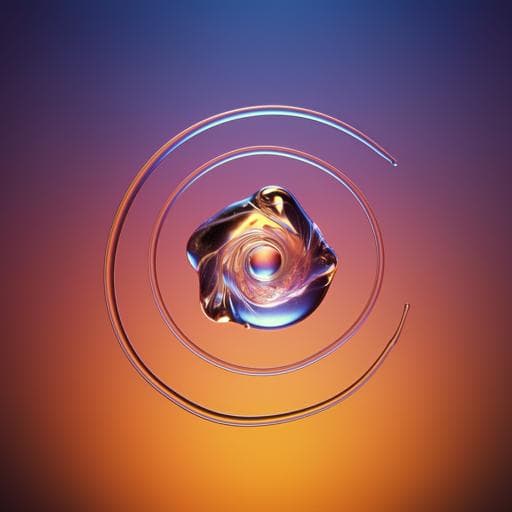
Engineering and Technology
Angle-programmed tendril-like trajectories enable a multifunctional gripper with ultra-delicacy, ultrastrength, and ultraprecision
Y. Hong, Y. Zhao, et al.
Discover the groundbreaking advancements in soft gripper technology developed by Yaoye Hong, Yao Zhao, Joseph Berman, Yinding Chi, Yanbin Li, He Huang, and Jie Yin. This innovative gripper can handle the most delicate tasks, from grasping fragile liquids to lifting objects 16,000 times its weight, all while integrating seamlessly with robotic arms. The possibilities are endless!
Playback language: English
Introduction
The development of versatile robotic grippers is crucial for advancing applications in diverse fields such as biomedicine, deep-sea exploration, agriculture, food processing, minimally invasive surgery, and prosthetics. Current grippers often struggle to meet the stringent demands of these applications, requiring specialized tools for different tasks. For instance, bio-fluidic manipulation needs ultra-delicate grippers to handle fragile objects like droplets, while minimally invasive surgeries demand soft grippers with high delicacy, strength, and precision. Similarly, ideal robotic prosthetics require grippers that mimic the dexterity, precision, and load-carrying capacity of human hands, while also being lightweight and easily integrable. Existing pneumatic or hydraulic grippers often present challenges due to their bulky systems.
The inherent tradeoff between delicacy, strength, and precision in soft grippers is a significant obstacle to overcome. While softness enhances delicacy, it compromises strength and precision, leading to low payload-to-weight ratios in many existing designs. Researchers have explored various strategies to bridge this gap, such as suction, fluid-driven rigidity percolation, and varied stiffness materials. However, these approaches often sacrifice delicacy or precision. For example, suction-based grippers cannot noninvasively grasp gelatinous organisms. Precise grasping of tiny or thin objects also remains a challenge. Kirigami-inspired grippers have shown promise but haven't fully addressed the need for a single gripper capable of handling extremely delicate, ultra-heavy, and micro-sized objects.
Mimicking the grasping mechanisms of natural organisms, such as cucumber tendrils and cephalopod tentacles, provides a potential solution. These organisms achieve a balance between delicacy and strength through nastic trajectories. While soft grippers often mimic the shapes of these organisms, they rarely leverage the nastic trajectory for enhanced grasping capabilities. Prior studies have primarily focused on adaptive morphologies, neglecting the crucial influence of grasping trajectories, especially in noninvasive manipulation and precision grasping of small or thin objects.
This research addresses these limitations by combining adaptive kirigami morphologies with the nastic curves observed in tendril plants. The goal is to design an angle-based kirigami gripper that can handle a wide range of tasks by manipulating the intersecting angle of its X-shaped ribbon. The resulting gripper offers unprecedented capabilities compared to state-of-the-art soft grippers. It enables programmable tendril-like trajectories, and achieves ultragentle yet ultrastrong and ultraprecise manipulations.
Literature Review
Existing literature on soft robotic grippers highlights a significant challenge: balancing delicacy, strength, and precision. Early research focused on using fluid-driven soft actuators, underactuated compliant elastomers, origami/kirigami structures, and stimuli-responsive materials. While softness allows for adaptability and delicate handling of fragile objects, it often limits the gripper's strength and precision. Grippers based on dielectric elastomer actuators (DEAs) have shown success in handling fragile items like eggs, but their payload-to-weight ratios are low. Hydraulic ribbon-based grippers can gently manipulate jellyfish, but their strength is limited.
Attempts to improve strength often involve suction, fluid-driven rigidity percolation, or varied stiffness materials. Suction cups, while effective for some objects, are inappropriate for delicate, non-invasive applications. Shape memory polymer-based grippers have demonstrated impressive payload-to-weight ratios, but at the cost of delicacy. Kirigami-based grippers have addressed some of these challenges, particularly in terms of precise handling of small objects and shape-morphing capabilities. However, existing kirigami designs often fall short in terms of achieving a true balance of the three key characteristics. The development of grippers capable of handling a broad range of objects across the stiffness, size, and weight spectrums remains an open challenge.
Methodology
This study presents a novel angle-based kirigami gripper design. The gripper is fabricated by laser cutting a thin polyethylene terephthalate (PET) sheet, creating a central X-shaped ribbon network that dictates the gripper's behavior. The intersecting angle (ψ₀) of this X-shaped ribbon is a crucial design parameter, allowing for the programming of the gripper's trajectory. By manipulating ψ₀, the gripper's movement can be controlled explicitly and predictably.
The researchers combined analytical analysis, experiments, and finite element method (FEM) simulations to investigate the gripper's behavior. An analytical model based on Euler elastica was developed to predict the gripper's trajectory based on the initial angle ψ₀ and applied strain. This model provides explicit relationships between the applied strain, the intersecting angle, and the curvature of the trajectory. The experimental setup involved uniaxial stretching tests using an Instron 5944 machine to measure force-displacement curves. The touch force and pulling-out force were also measured. FEM simulations in Abaqus were used to further validate the analytical model and explore the gripper's mechanical behavior.
The gripper's performance was evaluated across a wide range of objects, including water droplets, ultrathin polymer sheets and fibers, and heavy dead weights. The contact pressure exerted on delicate objects was measured to assess the gripper's gentleness. The payload-to-weight ratio was calculated to quantify the gripper's strength. The success rate of grasping different objects was recorded to evaluate the gripper's precision and reliability.
Finally, the gripper was integrated with a commercially available robotic arm (Robotiq 2F-85) and an electromyographic (EMG)-controlled prosthetic hand to demonstrate its adaptability and functionality in realistic scenarios. The control strategy for the prosthetic hand involved using EMG signals from the wrist extensor and flexor muscles to control the gripper's opening and closing.
Key Findings
The study's key findings demonstrate the superior performance of the angle-programmed kirigami gripper. The researchers successfully programmed the gripper's tendril-like trajectories by manipulating the initial intersecting angle (ψ₀) of the X-shaped ribbon. The analytical model accurately predicted the gripper's trajectories, showing a direct correlation between ψ₀ and the trajectory's curvature. A smaller ψ₀ resulted in a curlier trajectory, resembling the shape of a cucumber tendril.
The gripper exhibited exceptional capabilities across different manipulation tasks. It achieved ultra-gentle grasping of extremely soft objects, with a contact pressure as low as 0.05 kPa when handling a water droplet. This is comparable to the gentlest grippers reported in the literature. The gripper's ultra-strength was demonstrated by its ability to lift a dead weight 16,000 times its own weight, significantly exceeding the record payload-to-weight ratio of existing soft grippers. Moreover, the gripper achieved ultra-precision grasping of ultrathin objects, successfully handling 4-µm thick sheets and 2-µm diameter microfibers.
The gripper's design is highly versatile and material-independent. Biodegradable grippers were successfully fabricated using natural leaves, showcasing the potential for environmentally friendly soft robotics. The gripper's integration with a robotic arm and a prosthetic hand demonstrated its effectiveness in diverse real-world scenarios, including picking grapes, opening zippers, folding clothes, and turning book pages. In each scenario, the gripper's unique tendril-like trajectory minimized damage to the objects being manipulated, highlighting its superior handling of uncertainties and variability in delicate tasks. The success rate of these complex tasks (95.2% for folding garments and 78.6% for picking grapes) underscore the gripper's reliability and practicality.
Discussion
This study successfully addresses the long-standing challenge of creating a soft gripper that excels in both delicacy and strength, while also maintaining high precision and versatility. The angle-programmed tendril-like grasping trajectory is the key innovation. By controlling the initial angle (ψ₀), researchers can precisely manipulate the trajectory's curvature, creating a gripper that can adapt to objects with varying stiffness, size, and shape. The close-to-180-degree grasping angle, combined with the smooth, spherical shape of the petals when closed, allows for gentle encapsulation of objects.
The study's findings significantly advance the field of soft robotics, providing a potential solution for numerous real-world applications. The gripper's ability to handle both extremely delicate and ultra-heavy objects opens doors for advancements in biomedical devices, minimally invasive surgeries, and delicate manipulation tasks in diverse industrial settings. The design's scalability and material-independence further expand its potential, allowing for the creation of customized grippers suited to specific needs. The successful integration with both robotic arms and prosthetic hands showcases the potential for the gripper to be implemented in a variety of robotic systems.
The demonstrated ability to use biodegradable materials, like leaves, underscores the gripper's potential for environmentally conscious applications, minimizing waste and promoting sustainability.
Conclusion
This research presents a groundbreaking angle-based kirigami gripper that overcomes the limitations of existing soft grippers by incorporating programmable tendril-like trajectories. The gripper's exceptional performance in handling objects of varying stiffness, size, and weight opens up new possibilities for soft robotics in a wide array of applications. The study's success in integrating the gripper with robotic arms and prosthetic devices highlights its practical potential. Future research could explore optimizing the gripper's design for even greater durability, exploring different materials for enhanced strength and longevity, and investigating advanced control strategies for further refinement of its capabilities.
Limitations
While the study demonstrates the remarkable capabilities of the angle-programmed kirigami gripper, certain limitations exist. The current design's performance is affected by the relative size of the target object. Very large objects might prevent complete encapsulation, potentially leading to pinching and reduced pulling-out force. Future research could focus on addressing these limitations and exploring modifications to improve handling of oversized targets. Also, material properties influence the gripper's strength and durability. While the use of biodegradable materials is a significant advantage, exploring materials with greater Young's modulus and fracture toughness would enhance overall performance. Finally, further studies are necessary to extensively evaluate the gripper's long-term reliability and durability under various operating conditions and stresses.
Related Publications
Explore these studies to deepen your understanding of the subject.