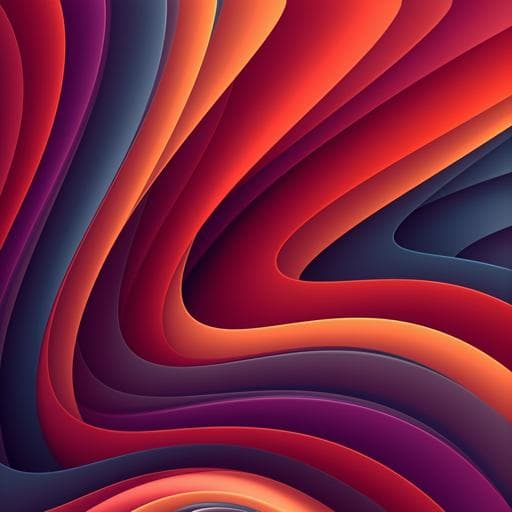
Engineering and Technology
Ultra-sensitive, highly linear, and hysteresis-free strain sensors enabled by gradient stiffness sliding strategy
F. Xue, Q. Peng, et al.
Researchers have made a breakthrough in strain sensor technology with a gradient stiffness sliding design strategy, achieving a remarkable gauge factor of 9.1 × 10⁴ and an impressive linearity of R² = 0.9997. This study, conducted by Fuhua Xue, Qingyu Peng, Renjie Ding, Pengyang Li, Xu Zhao, Haowen Zheng, Liangliang Xu, Zhigong Tang, Xinxing Zhang, and Xiaodong He, opens the pathway for ultra-high sensitivity and linearity in various sensing applications.
Playback language: English
Related Publications
Explore these studies to deepen your understanding of the subject.