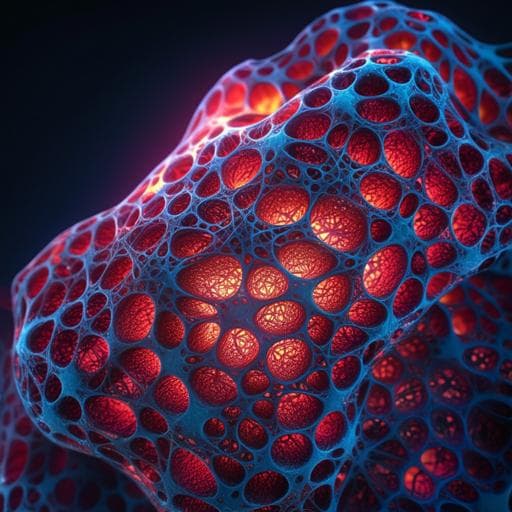
Engineering and Technology
Nano-topology optimization for materials design with atom-by-atom control
C. Chen, D. C. Chrzan, et al.
Discover the groundbreaking "Nano-Topology Optimization (Nano-TO)" method developed by Chun-Teh Chen, Daryl C. Chrzan, and Grace X. Gu, enabling the design of nanostructured materials with unparalleled elastic properties. This innovative approach outperforms existing TPMS structures and the Hashin-Shtrikman upper bound, paving the way for novel materials without predetermined designs.
Playback language: English
Related Publications
Explore these studies to deepen your understanding of the subject.