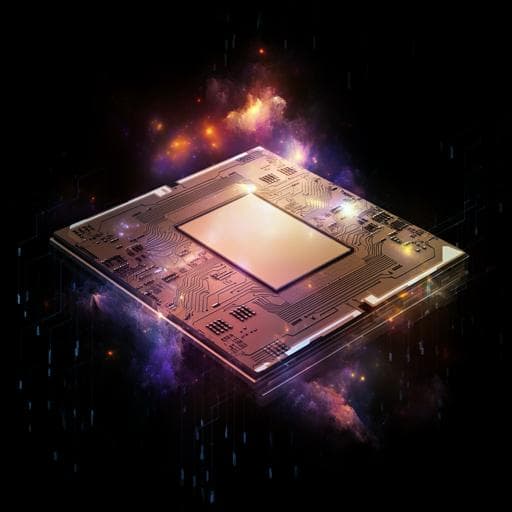
Engineering and Technology
Human-machine collaboration for improving semiconductor process development
K. J. Kanarik, W. T. Osowiecki, et al.
This groundbreaking research by Keren J. Kanarik and colleagues from Lam Research Corporation explores the application of Bayesian optimization algorithms in semiconductor chip fabrication. Discover how a hybrid strategy combining human expertise with computer efficiency significantly reduces costs while overcoming cultural challenges in collaboration.
Playback language: English
Related Publications
Explore these studies to deepen your understanding of the subject.