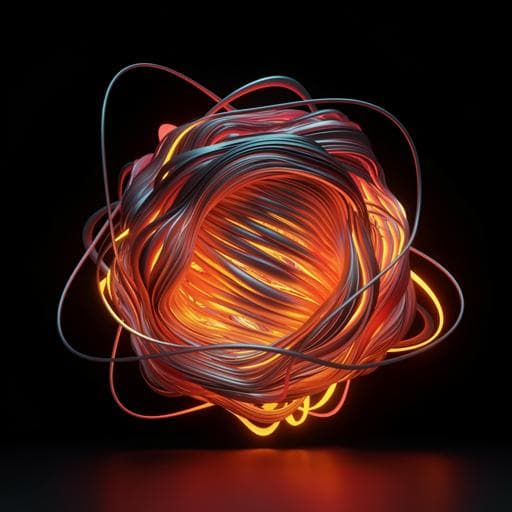
Engineering and Technology
Generalisable 3D printing error detection and correction via multi-head neural networks
D. A. J. Brion and S. W. Pattinson
Discover how Douglas A. J. Brion and Sebastian W. Pattinson have developed CAXTON, a cutting-edge system utilizing a multi-head neural network to automatically detect and correct errors in material extrusion. This innovative approach leverages a massive dataset of 1.2 million images to enhance the quality of additive manufacturing processes!
Playback language: English
Related Publications
Explore these studies to deepen your understanding of the subject.