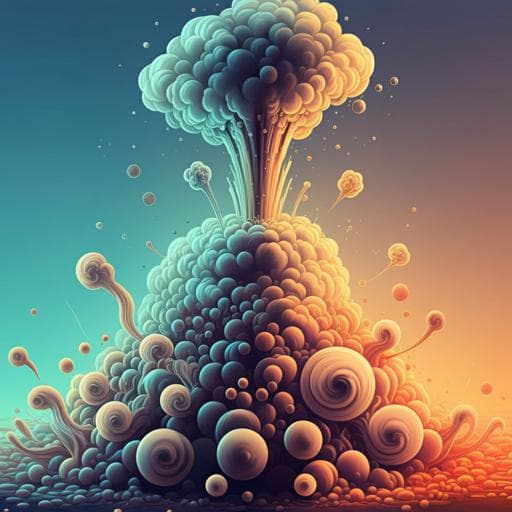
Chemistry
Catalytic polymer self-cleavage for CO₂ generation before combustion empowers materials with fire safety
W. Luo, M. Chen, et al.
Discover an innovative approach to enhancing fire safety in polymeric materials through catalytic polymer auto-pyrolysis. Conducted by Wei Luo, Ming-Jun Chen, Ting Wang, Jin-Feng Feng, Zhi-Cheng Fu, Jin-Ni Deng, Yuan-Wei Yan, Yu-Zhong Wang, and Hai-Bo Zhao, this study reveals how potassium salts can transform polyurethane foam to generate CO₂ effectively, providing an internal fire extinguishing mechanism while lowering smoke toxicity.
Playback language: English
Related Publications
Explore these studies to deepen your understanding of the subject.