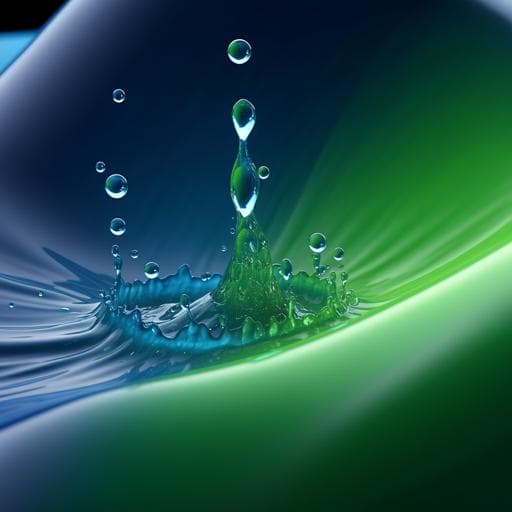
Engineering and Technology
Bipolar membrane electrolyzers enable high single-pass CO2 electroreduction to multicarbon products
K. Xie, R. K. Miao, et al.
Discover groundbreaking research from a talented team including Ke Xie and Rui Kai Miao, which presents a novel CO2 electrolyzer leveraging a bipolar membrane to enhance CO2 conversion efficiency. This innovative approach achieves a remarkable 78% single-pass CO2 utilization, significantly reducing energy consumption in downstream separation.
Playback language: English
Introduction
The electrochemical reduction of carbon dioxide (CO2RR) offers a promising pathway for converting renewable electricity into valuable multicarbon (C2+) products, such as ethylene and ethanol. However, current CO2RR technologies face significant challenges, primarily concerning energy efficiency and CO2 utilization. In conventional alkaline and neutral membrane electrode assembly (MEA) CO2 electrolyzers, the CO2 reactant rapidly reacts with hydroxide ions (OH-) to form bicarbonate (HCO3-) and carbonate (CO32-), leading to substantial energy losses associated with separating CO2 from the anode off-gases. This separation is energy-intensive, making the overall process less economically viable. The single-pass CO2 utilization (SPU) in these systems is often limited, requiring significant recycling of unreacted CO2, adding further complexity and cost. Previous attempts to improve SPU in neutral-media electrolyzers have been hampered by the 25% limit for C2+ product formation. This research addresses these limitations by introducing a novel CO2 electrolyzer design that significantly improves both energy efficiency and CO2 utilization. The core innovation lies in the strategic use of a bipolar membrane (BPM) to regenerate CO2 in situ near the cathode, thus preventing crossover and enhancing the availability of the reactant for CO2RR. This approach not only minimizes the need for energy-intensive CO2 separation but also drastically improves SPU.
Literature Review
Existing literature extensively documents the challenges of CO2RR in alkaline and neutral media. Studies like those by Dinh et al. (Science, 2018) and Gabardo et al. (Joule, 2019) highlighted the significant energy penalty associated with (bi)carbonate formation and the subsequent separation of CO2 from the anode stream. These works underscored the need for novel strategies to improve single-pass CO2 utilization and reduce energy consumption. Efforts to mitigate (bi)carbonate formation have included the use of solid-state polymer electrolytes (Ma et al., Chem. Sci., 2020) and bipolar membranes (Vermaas & Smith, ACS Energy Lett., 2016; Yang et al., ACS Energy Lett., 2021). While bipolar membranes have demonstrated their potential in blocking CO2 crossover, challenges remain in terms of cathode acidification and inefficient CO2 regeneration near the CEL. Previous BPM-based electrolyzers (Table 1 in the original paper) have typically achieved only modest SPU values for C2+ electroproduction, generally below 15%. This study builds upon these previous efforts, addressing the limitations of existing BPM designs and achieving significantly higher SPU.
Methodology
The researchers developed a novel CO2 electrolyzer design incorporating a bipolar membrane (BPM) and a stationary, unbuffered catholyte layer. The BPM facilitates the conversion of (bi)carbonate back to CO2 near the cathode, preventing CO2 crossover to the anode and enhancing reactant availability. A key element of their approach involves the strategic design of the catholyte layer's thickness. They employed a one-dimensional multiphysics model in COMSOL to investigate the influence of catholyte composition and thickness on local pH, CO2 regeneration efficiency, and overall cell performance. The model considered various thicknesses (16 µm, 65 µm, 125 µm, and 250 µm) and catholyte compositions (0.5 M K2SO4 and KHCO3). The simulations examined the interplay between CO2 diffusion, proton migration, and CO2 regeneration, guiding the optimal design parameters. The cathode was prepared by spraying Cu nanoparticles onto a hydrophobic carbon gas-diffusion layer, and the anode comprised IrO2 supported on Ti felt. A custom BPM, incorporating TiO2 nanoparticles as a water dissociation catalyst, was used to minimize voltage loss. Electrochemical measurements were performed to assess the cell voltage, Faradaic efficiency (FE) for different products (H2, CO, CH4, C2H4, etc.), and single-pass CO2 utilization (SPU) at various current densities and CO2 flow rates. Gas and liquid products were analyzed using gas chromatography and proton nuclear magnetic resonance spectroscopy (1H NMR), respectively. Furthermore, the authors conducted a comprehensive energy assessment, comparing their system to state-of-the-art CO2-to-ethylene electrolyzers. This assessment incorporated the costs of electrolysis electricity, cathodic and anodic stream separation.
Key Findings
The study's key findings revolve around the successful design and demonstration of a high-performance CO2 electrolyzer. Their COMSOL simulations revealed a critical relationship between the catholyte layer thickness and CO2 mass transport. Optimally, a thin, unbuffered catholyte layer (around 65 µm) balanced CO2 diffusion flux with regeneration rate, promoting C2+ product formation and minimizing energy losses. This thickness ensured a high local cathode pH (>11) while maintaining efficient CO2 transport. The use of a custom BPM significantly reduced cell voltage compared to commercial BPMs. Experimental results confirmed the effectiveness of this design, showing a substantially reduced anode CO2/O2 ratio (0.06 at 200 mA cm-2) compared to conventional AEM-based MEAs, indicating minimal CO2 crossover. The 65 µm catholyte layer SC-BPMEA achieved an unprecedented single-pass CO2 utilization of 78% at 200 mA cm-2, representing a 10-fold improvement over previous neutral-media electrolyzers. This high SPU is accompanied by a reasonable ethylene FE (42%) and a cell voltage (3.8 V) comparable to the best conventional neutral-electrolyte CO2-to-ethylene MEAs. The energy analysis revealed that the SC-BPMEA's energy intensity for ethylene production is significantly lower than that of other CO2-to-ethylene electrolyzers, primarily due to the drastically reduced energy penalty associated with CO2 separation (Table 3). This is because CO2 crossover was less than 0.5% of the total input CO2. The authors investigated the impact of the catholyte layer thickness on CO2RR performance; thinner layers (16 µm) resulted in lower CO2RR selectivity, while thicker layers (250 µm) suffered from increased ohmic losses and lower SPU. The electrolyzer exhibited stable operation for over 50 hours at 200 mA cm-2 under limited CO2 availability.
Discussion
The research successfully addresses a critical challenge in CO2RR: the energy penalty associated with (bi)carbonate formation and CO2 separation. By employing a BPM and strategically designing a thin, unbuffered catholyte layer, the authors have achieved remarkably high single-pass CO2 utilization (78%) without sacrificing performance metrics such as cell voltage and ethylene FE. The significantly reduced CO2 crossover minimizes the energy cost associated with anodic separation, leading to a substantial decrease in the overall energy intensity for ethylene production compared to existing technologies. The results highlight the importance of controlling the local microenvironment near the cathode to optimize CO2 mass transport and reaction kinetics. The findings have broad implications for the field of CO2RR, suggesting a viable pathway towards economically viable electrochemical conversion of CO2 into valuable chemicals. The demonstrated stability suggests potential for scalability and practical implementation.
Conclusion
This research demonstrates a significant advancement in CO2 electroreduction technology. The developed SC-BPMEA electrolyzer overcomes the limitations of conventional systems by effectively managing (bi)carbonate formation and minimizing CO2 crossover, leading to unprecedented single-pass CO2 utilization (78%). The superior energy efficiency compared to other CO2-to-ethylene electrolyzers positions this technology as a promising candidate for large-scale CO2 conversion. Future research could focus on further optimizing the catholyte layer composition, exploring alternative BPM materials with even lower voltage losses, and investigating novel high-performance catalysts. This system could also serve as a platform for studying other electrochemical processes where controlling microenvironments and species transport are crucial.
Limitations
While the study achieves remarkable results, some limitations are worth noting. The energy assessment relies on modeling, and while the model is based on established approaches, uncertainties inherent in such models exist. The study primarily focuses on ethylene production, and the generalizability to other C2+ products requires further investigation. The custom BPM used in the study might not be readily available commercially, and its long-term stability under industrial-scale operating conditions needs further evaluation. The optimization of the catholyte layer is limited to the specific materials and thicknesses examined; other possible configurations warrant exploration. Further exploration of the system's long-term stability and performance at higher current densities would strengthen the claims of its practical applicability.
Related Publications
Explore these studies to deepen your understanding of the subject.