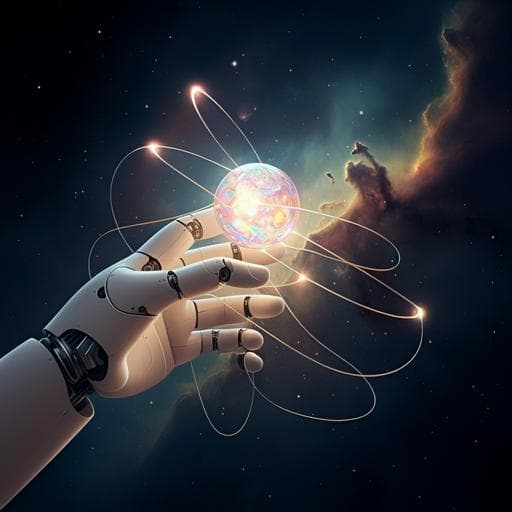
Engineering and Technology
A supertough electro-tendon based on spider silk composites
L. Pan, F. Wang, et al.
Discover the groundbreaking development of a supertough electro-tendon made from spider silk composites, capable of enhancing the design of humanoid robotic hands. This innovative research, conducted by Liang Pan, Fan Wang, Yuan Cheng, Wan Ru Leow, Yong-Wei Zhang, Ming Wang, Pingqiang Cai, Baohua Ji, Dechang Li, and Xiaodong Chen, reveals an electro-tendon that combines both strength and conductivity, revolutionizing robotic applications.
Playback language: English
Related Publications
Explore these studies to deepen your understanding of the subject.